You are here
Back to topHow Emerson is Delivering an "End-to-End" Cold Chain Solution to Customers in Asia
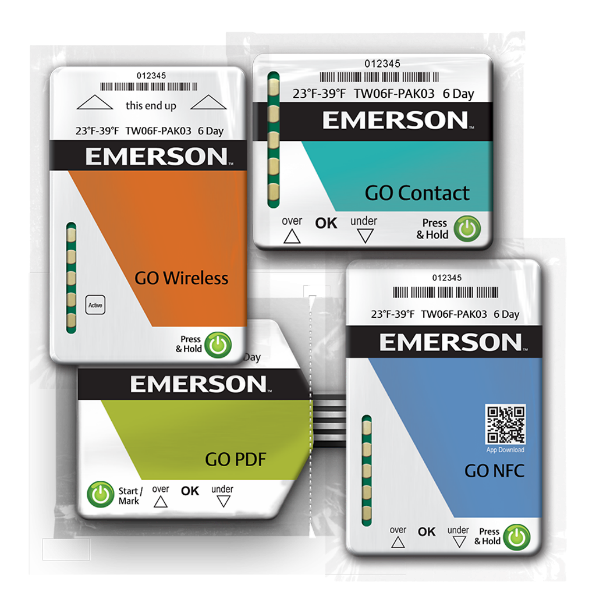
Emerson Cargo Solutions' "GO" line of logging devices
Founded in 1890 and with more than $15 billion in annual revenue, Emerson is one of those enormous companies about which average consumers may know little or nothing, but which, through its role as a b2b supplier, is actually hugely important to the production of a wide range of products and services that consumers use every day.
This is certainly the case for the fresh produce industry. Since the acquisition of the compressor and refrigeration systems company Copeland in 1986, US-headquartered Emerson has steadily grown its stable of products and services for cold chain infrastructure and management, offering these products to fresh produce growers, distributors, logistics providers and retailers around the world.
Emerson’s main R&D center for HVAC and cold chain, “The Helix”, is located in Dayton, Ohio, USA, and, “contains a total of five real-world simulated environments, including a fully-functioning and furnished home, a model supermarket, a light commercial environment, a commercial kitchen and a data center,” for developing and testing refrigeration technologies, according to a company statement. “These modules provide a sandbox for rapid prototyping and practical applications and we use them to help develop our next generation products.”
Traditionally, Emerson has focused on the cold chain infrastructure. But with the strategic acquisition of three companies in the past few years, Emerson has launched a new business unit called Cargo Solutions, which provides logging and tracking solutions for the products themselves that are moving through the cold chain.
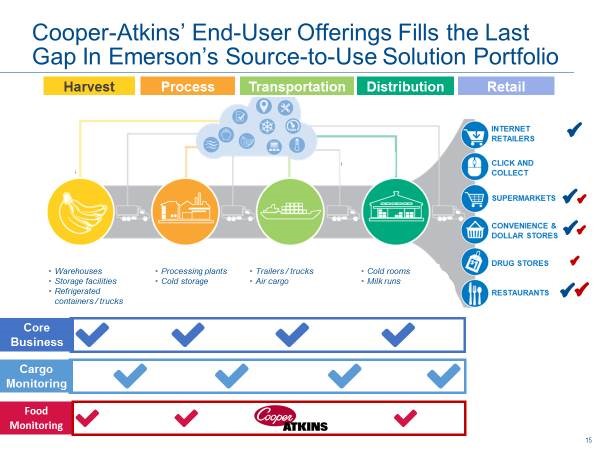
The company thinks these products have big growth potential in coming years in Asia, and especially China. Emerson therefore exhibited for the third straight year at the Asia Fruit Logistica fresh produce trade show in Hong Kong earlier this month to showcase new products developed especially for the Asian market. Produce Report sat down with Frank Landwehr, Vice President and General Manger for Emerson Cargo Solutions, and Ivan Fullin, Director for Emerson Cargo Solutions- Asia, to learn more about how Emerson is helping its Asian customers improve their cold chain management in order to improve quality, ensure safety, and save money.
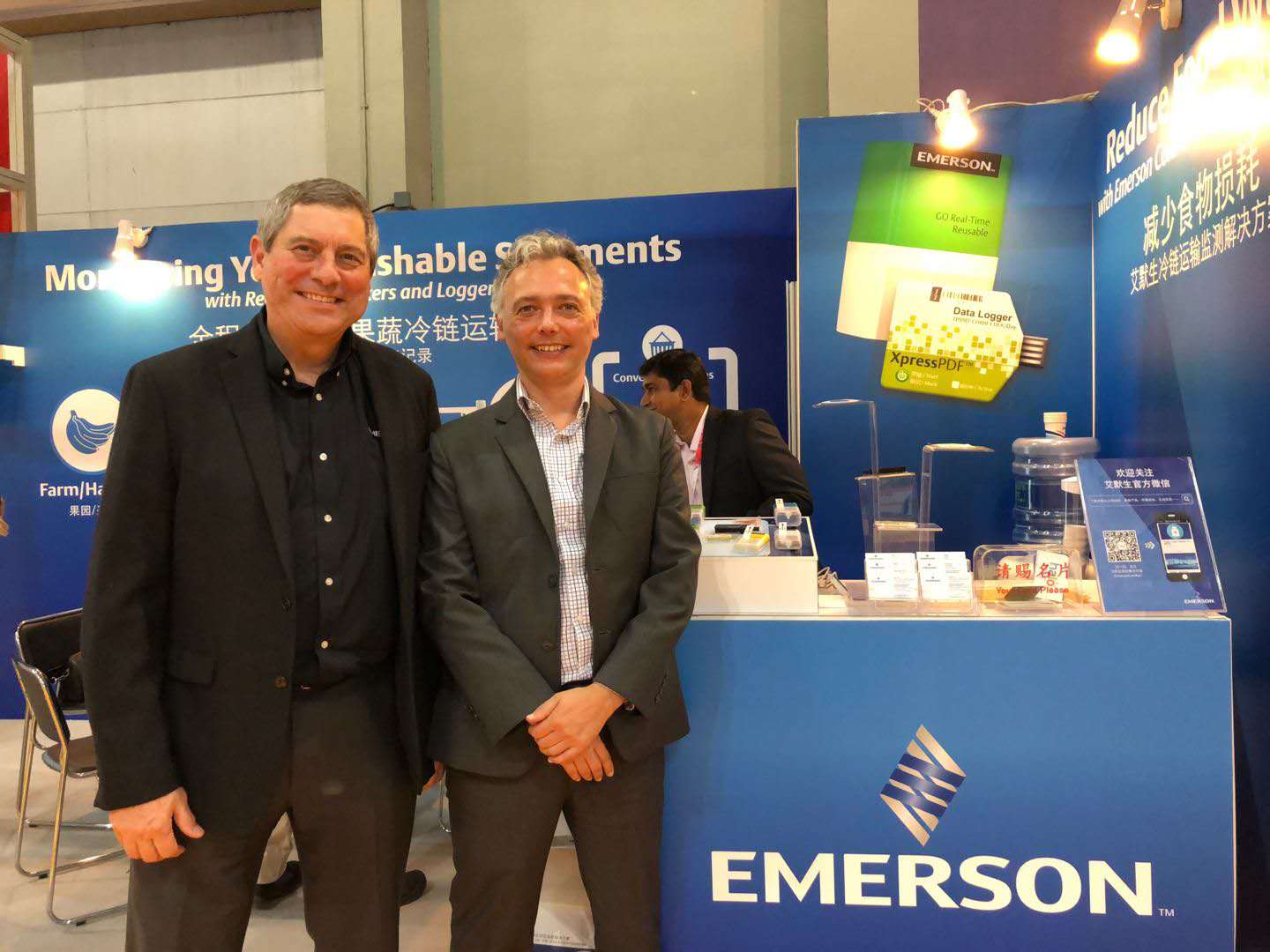
Emerson has already been in Asia for decades. In China, where it first set up operations in 1996, Emerson has three manufacturing facilities for HVAC and cold chain, as well as R&D, customer service and training centers. The cold chain part of Emerson’s business has been picking up in China in recent years as the food industry has sought to upgrade its cold chain infrastructure, say Landwehr and Fullin. Fullin says that, “Emerson already works with the majority of the large domestic and international produce retailer chains in China to offer monitoring solutions.”
Now, after completing the acquisition of companies Cooper-Atkins, Locus Traxx and PakSense, Emerson has integrated those companies’ products and services into Emerson’s other cold chain solutions businesses, creating a comprehensive in-transit and in-storage monitoring solution, which give suppliers, retailers and logistics companies the ability to see what happens to shipments of fresh produce at every step from harvest to the final consumer.
“Upon launching the Cargo Solutions business, it became the first time Emerson is monitoring temperature and other parameters directly on the produce itself,” says Landwehr. “This step completed Emerson’s ability to deliver end-to-end cold chain solutions.”
The key products for the in-transit part of this process are devices called loggers, which passively store data until the shipment arrives and trackers, which use wireless technology to broadcast data in real time. Emerson logger data can be offloaded in a variety of ways, including models that support NFC and wireless transmission. Depending on the device model, data that can be captured includes temperature, time in-transit, humidity, light and location.
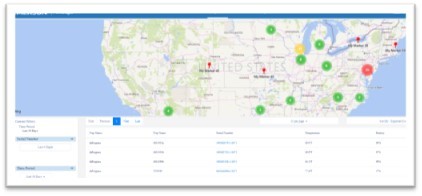
When this data is transmitted from a real-time tracker or offloaded from a logger, it can be processed, stored and analyzed on Emerson’s proprietary cloud software called Oversight, which allows customers to tie together data from trackers, loggers and other sensors located in pre-cooling facilities, warehouses and/or retail facilities. “With our wireless technology loggers, when a truck is pulling up to a distribution center, even when it is still 100 meters away, the trip data has already been uploaded to the cloud,” says Fullin. Emerson Cargo Solution’s service team can also provide custom reporting and help customers integrate sensor data into their own software systems, such as Transportation Management Systems.
Fullin says that for the moment most of the customers in China for these products are importers and exporters. Emerson has even developed new versions of its GO line of loggers with extended data storage (up to 110 days) and temperature ranges based on the needs of Chinese customers exporting frozen seafood to South America. But interest is picking up in China for other applications, such as monitoring shipments between farms and various distribution centers.
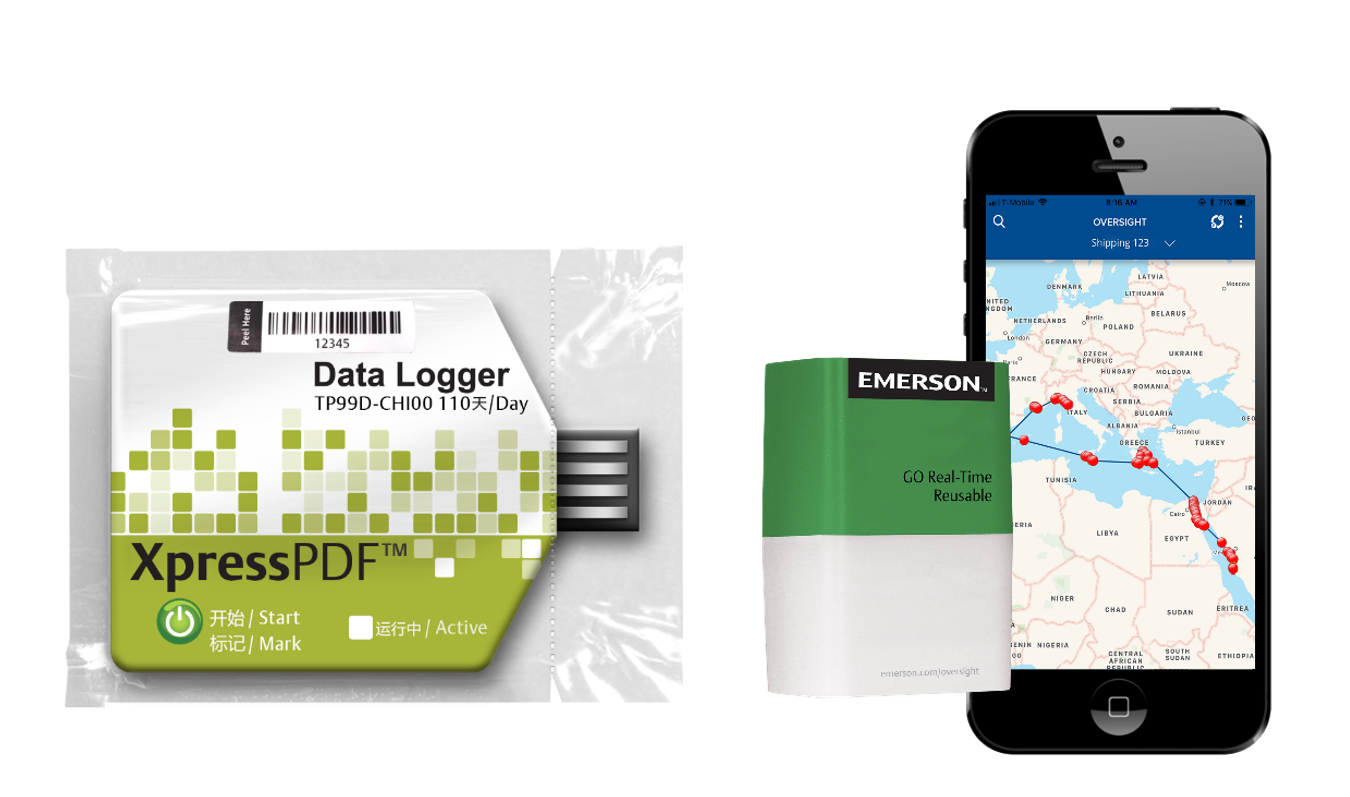
“It’s a natural part of the evolution of cold chain management in China that our customers here are moving beyond cold storage infrastructure and are now placing more emphasis on what’s happening during the transportation of the food,” says Fullin. “This is not only for quality and safety, but smarter cold chain management also saves our customers money.”
Of course, implementation of these practices is easier said than done, which is why Emerson is highly localized in global markets where it works, including in Asia, tailoring its products to customers’ needs and providing extensive customer service and online and on-site training. “We believe Emerson’s Cargo Solutions business is largely a service business,” says Landwehr. “We’re not just selling monitoring devices to the customer; we are also helping the customer to access and interpret the data to make good decisions. We have an onboarding process for new customers alongside comprehensive 24/7 support and ongoing training.”
Add new comment